What's Your Success?
RFID Warehouse Tracking Software
Scan thousands of items in seconds.
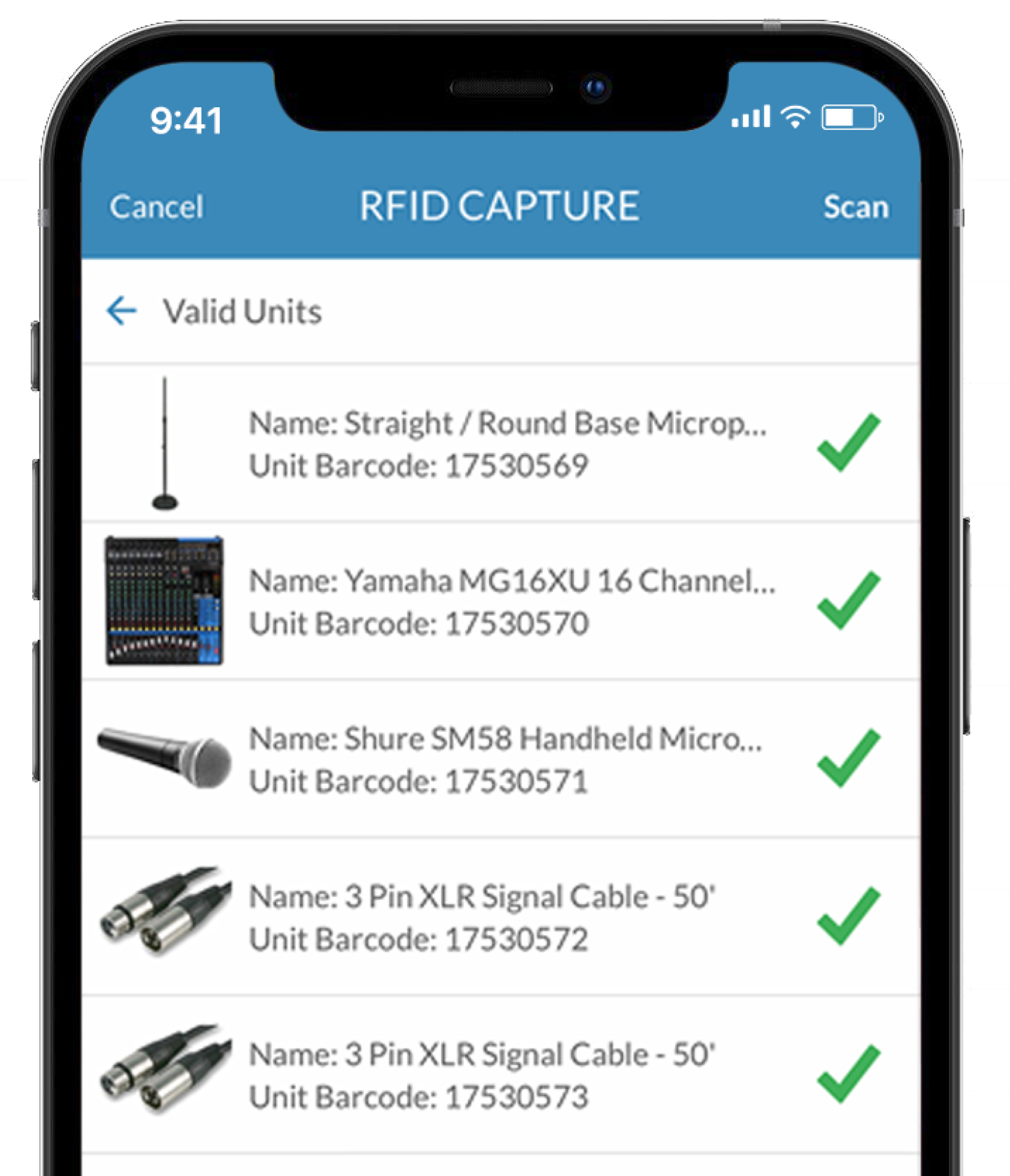
"RFID is probably cutting down our cable return time to maybe a third compared to barcode scanning. It’s saving us hours beyond what we anticipated."
Scan Less, Do More

Your favorite inventory tracking apps now come with RFID.

Real-time data accuracy

Reduce long-term costs of asset scanning

Move towards a more efficient warehouse

More time to focus on things other than scanning
See how it works.
Learn how Flex’s RFID Proof of Concept Kit can get you quickly started with an all-in-one package and watch Flex CEO Chris Stein review the latest in RFID technologies you’ll receive as part of the kit.

Recognize the benefits of RFID with Flex
Reduce Costs

Reduce Scan Time

Up to 10x Speed Improvement!

Flex RFID Webinar
Check out CEO Chris Stein’s webinar, RFID Is Finally Ready for its Close-Up, and discover how RFID will help your business become more efficient!
We know you’ve heard this before, “RFID will save you time and money!” Then what happens? It doesn’t. RFID just ends up being another empty promise that fails to deliver any ROI. It’s enough to make any organization skeptical. Because without major considerations and modifications, RFID best practices in other industries do not translate easily into the Live Event Industry workflow, RFID is the boy who cried wolf.
- But what if we could show you how to use Flex to implement RFID and build on warehouse best practice workflows without any change?
- What if we could show you how to balance speed, accuracy, and accountability? (Because, let’s face it, speed at the cost of accuracy is not a solution.)
- What if we could show you that RFID with Flex was really, truly, absolutely ready?
With improvements in the hardware and the overall environment, Flex CEO, Chris Stein, is more optimistic and more passionate than ever about how RFID can deliver value within our industry using existing best practices and workflows. Oh yeah, you’ll ultimately save time and money, too.
You can access the slideshow: Flex RFID Functionality for the Live Event Industry here.
Frequently Asked Questions

RFID technology boosts inventory management efficiency by quickly processing multiple items simultaneously—up to 100 tags at once—making it up to 10 times faster than traditional barcode scanning. This speed enhancement streamlines warehouse operations and reduces the time and effort needed for inventory tasks.
RFID technology in inventory management, while advantageous, faces challenges such as unintended tag reads due to its radio frequency operation without needing line-of-sight. This can lead to accidental scanning of nearby, unrelated tags. Effectiveness is also reduced when tags are tightly packed, like stacked cables, hindering accurate reads. To counter this, spreading items like cables before scanning and packing them is recommended for more reliable and accurate tag detection, minimizing the risk of missed or incorrect reads.
The Zebra RFD40 and RFD90 Premium Plus models, recommended for warehousing tasks, offer dual functionality of RFID reading and barcode scanning in one ergonomic device. Their dual-trigger design allows quick switching between RFID reading (top trigger) and barcode scanning (bottom trigger), enhancing operational speed and eliminating the need for multiple devices.
Flex recommends devices that combine RFID and barcode scanning for diverse warehouse needs. For items like microphones, where RFID is impractical, barcode scanning is preferred. The workflow includes using barcodes for case identification and closure, with RFID for item addition, enhancing packing efficiency. This dual-scanning approach also facilitates specific packing instructions, ensuring accurate storage or shipment preparation in complex warehousing scenarios.
The Zebra RFD90 and RFD40 models are both efficient, robust, and reliable for warehousing, offering high accuracy and functionality. The RFD90 has slightly better specs in range, durability, processing power, battery life, and connectivity. The choice between them depends on your specific warehousing needs, cost considerations, and desired features. The RFD90 is more durable, suitable for extreme conditions, has a faster processor for smoother operations, and a longer battery life, making it ideal for continuous, intensive use. Both models are strong choices for modern inventory management efficiency and accuracy.
When bought directly from Flex, the Zebra RFD40 and RFD90 scanners come ready-to-use with the Flex Mobile App, pre-updated with the latest firmware and default configurations for immediate optimal performance. If purchased elsewhere, contact Flex Support for necessary firmware updates and configurations to ensure full compatibility and optimization with the Flex Mobile App.
Flex maintains neutrality in recommending mobile devices for RFD scanners, though we have a preference for Apple. The crucial selection criteria are modernity and Bluetooth 5.3 compatibility, ensuring enhanced performance with RFD scanners due to faster data transmission. Choose devices with these features for the best results.
Flex’s RFID app is compatible with both iOS and Android platforms, working across mobile devices like smartphones and tablets, with an optimized user interface. It also supports newer Macs with Silicon M Series processors, offering versatility and convenience in managing RFID tasks across various devices and systems.
Currently, Flex’s RFID functions are limited to M Series Processor-powered laptops and desktops via the mobile app. However, we’re working on bringing these features directly to our Web-Based Desktop environment, compatible with browsers like Safari and Google Chrome. This expansion will enhance accessibility and utility across devices, demonstrating our dedication to evolving our solutions to meet user needs efficiently and user-friendly.
Flex is cautiously evaluating the integration of RFID portals for warehousing, mindful of challenges like ensuring full read rates and avoiding unintended scans. We prioritize providing users with real-time, accurate inventory data for immediate verification. While considering RFID portals’ potential benefits against their operational complexities, our current focus remains on direct, user-friendly inventory management solutions.
Yes we plan on implementing RFID in this area in the future.
Free Scan In Scans will return gear to the warehouse and mark the unit as returned from the last job. It is beneficial to use this when inventory from different jobs are intermingled. Best practice is to have the warehouse manager review the manifest to look for any discrepancies on unreturned items.
Yes, by opening the Free Scan In Page and doing an initial return.
Yes.
The scanners need a User Interface to interact with. Ideally they are connected to a mobile device running the Flex5 Mobile app. This allows the user to be untethered from workstations to work throughout the warehouse. Each user can work independently of one another, and still have audit-ability.
The Vizinex Tags have a better read range than most and are designed for cables. That does not guarantee 100% read range, especially stacked on top of each other and in cases. A workflow that would give better results is to read the cable before packing in the case during prep or after unpacking the case during return.
There are prompts that are presented to the user if an item needs review. See screenshots below. This unit was marked as Out of Commission on the job site by a user using the Flex App. Leave the Out of Commission checkbox as unmarked, scan it, and take it to your repair area.
Yes, in the QuickLink area use Inquiry Scan. This does not scan the item out or in, just opens it.
Our app does not support that, but there are specific Zebra apps that have a “Find My Tag” type feature. We do not have experience with that app and the TC21 when paired to the RFD40. Something to review more in the future.
Units counted and displayed in Invalid area are tags that are read that do not have an ID assigned to a unit in the system.
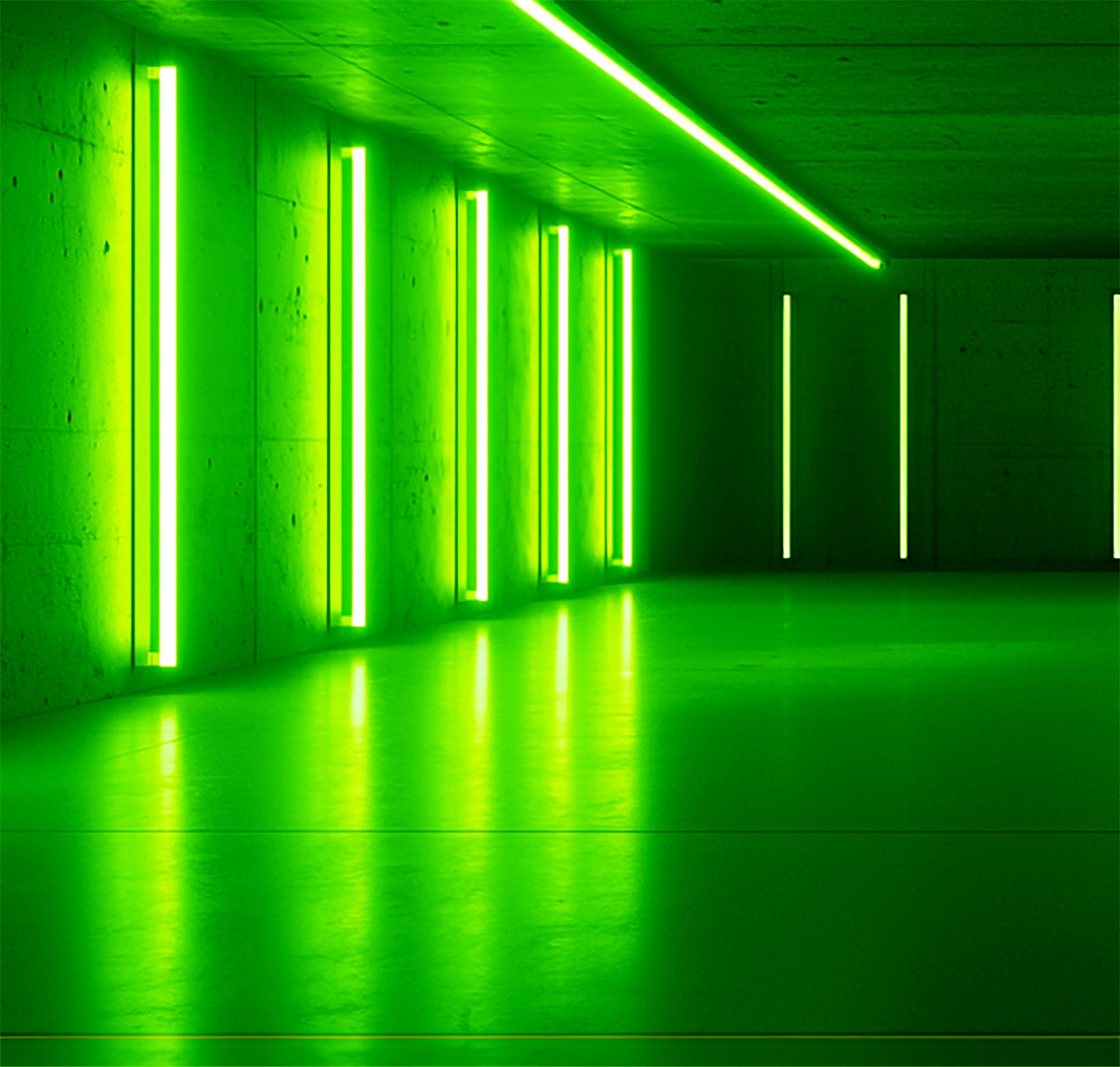
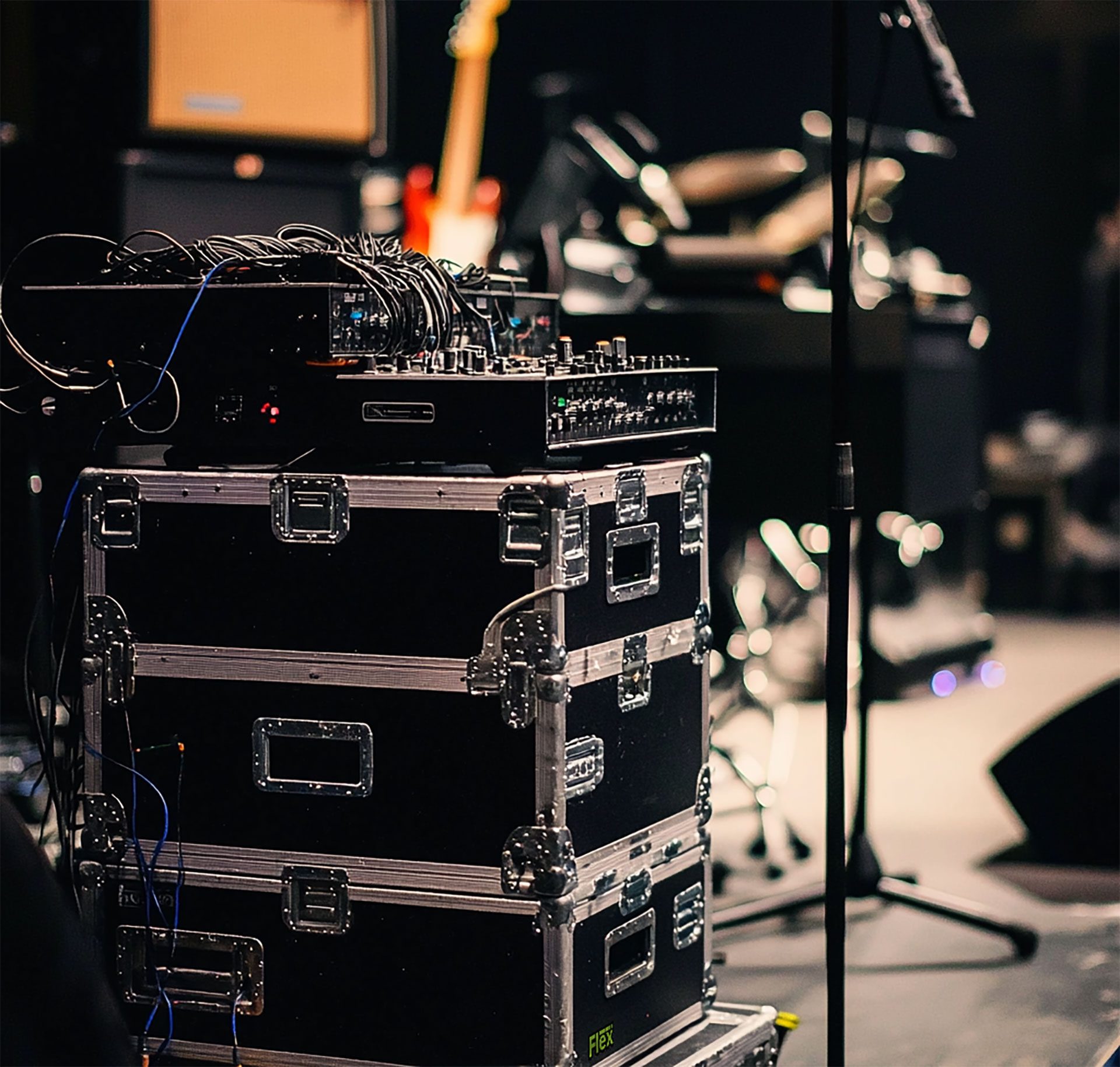
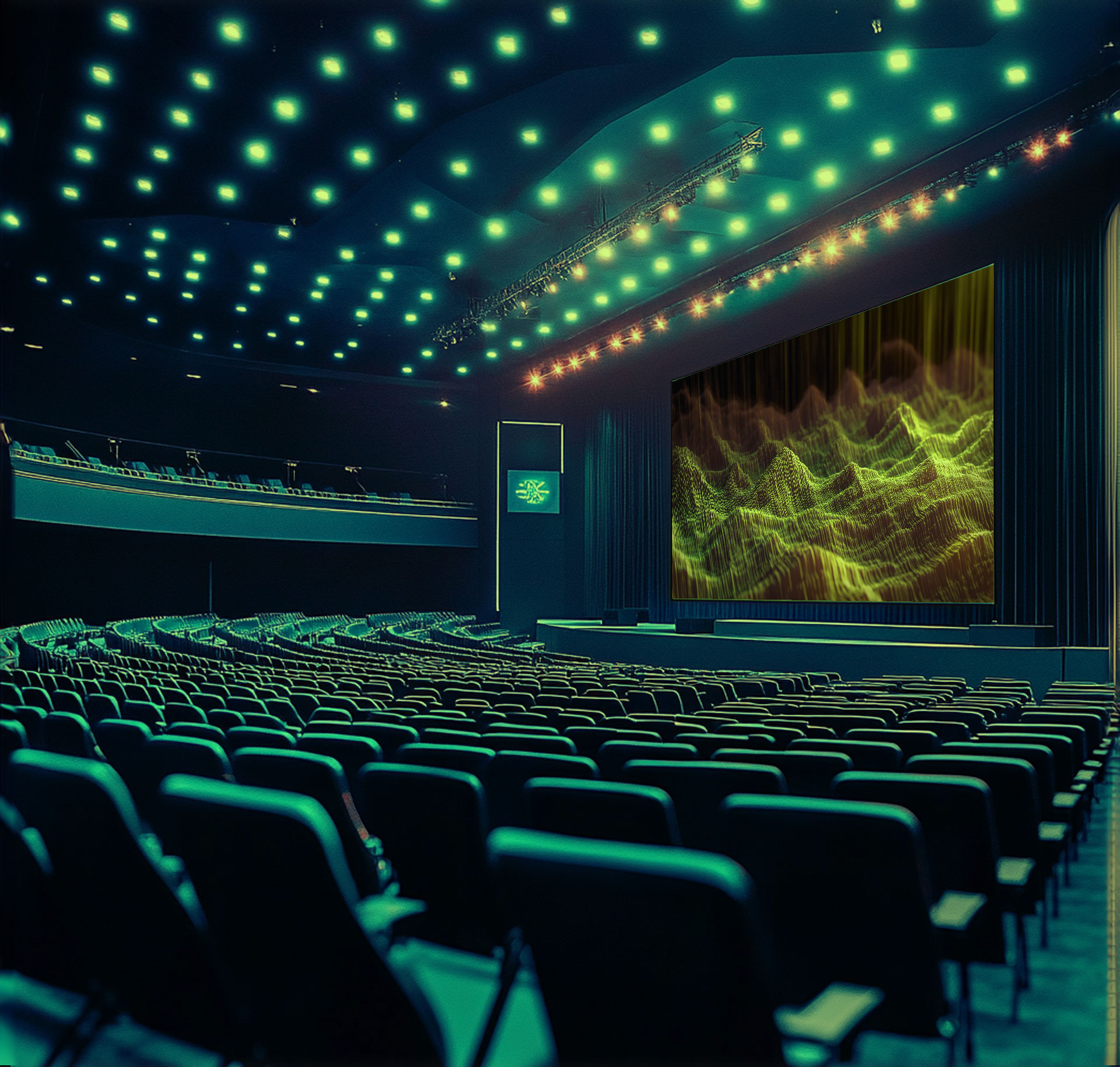
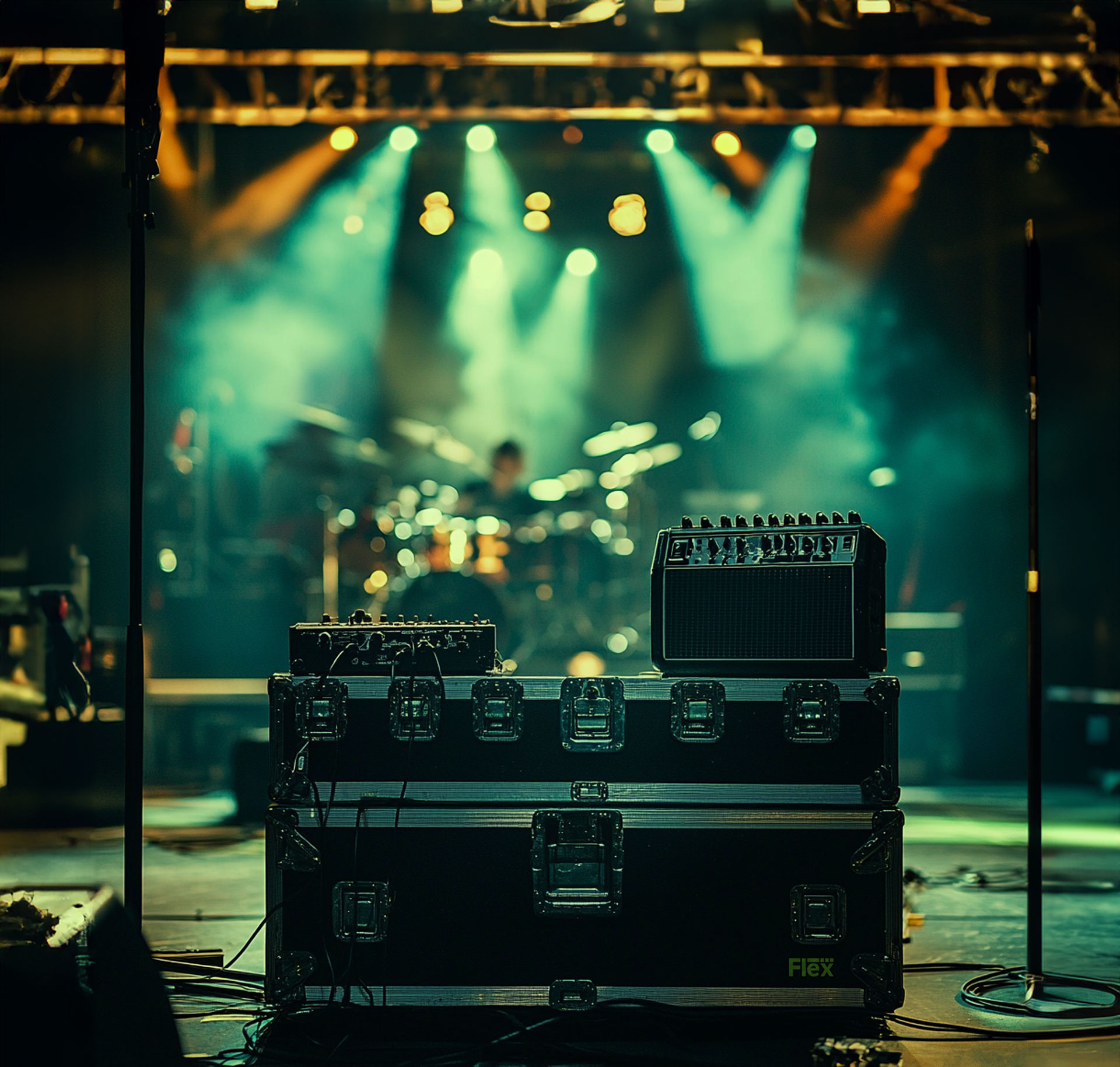